Integrated Multi-Pollutant Synergistic Ultra-Low Emission System with Ceramic Catalysts for Glass Melting Furnaces
Traditional Process (Glass & Industrial Furnaces)
EP (Dust Collection) + SCR (NOx Removal) + Desulfurization + Baghouse Filtration
Issues with Conventional Technology:
- Catalyst Poisoning & Clogging – High dust environment causes alkali metals (K, Na, Ca) in fly ash to deactivate catalysts, blocking flue gas channels and accelerating wear, leading to short service life.
- Ammonia Slip & Low Denitrification Efficiency – Excessive ammonia escape leads to ammonium bisulfate crystallization, creating a vicious cycle that threatens system stability and ultra-low emission compliance.
- Dust Clogging in ESP/Bag Filters – Ammonia slip reacts with SO₃ to form sticky ammonium salts, increasing system resistance, reducing fan efficiency, and impacting production capacity.
- Heat Exchanger Fouling in Waste Heat Boilers – Ash buildup reduces heat transfer efficiency, lowering boiler performance.
- High Failure Rate & Maintenance Costs – Frequent breakdowns affect production safety and economic efficiency, with high operational expenses.
Key Problems Solved
✅ System Efficiency – Overcomes limitations of traditional desulfurization, denitrification, and dust removal. The new process ensures high efficiency, reliability, and low-cost operation while maintaining adaptability to future emission standards.
✅ System Stability – Resolves low SCR denitrification efficiency and severe ammonia slip caused by tar, organic compounds, and ammonium sulfates, which lead to catalyst clogging, poisoning, and activity degradation.
✅ Low-Cost Operation – Eliminates secondary pollution from wet desulfurization wastewater and enables solid waste recycling. Prevents catalyst deactivation due to long-term low-temperature operation by incorporating periodic high-temperature regeneration without excessive cost increases.
✅ Maximized Economic Benefits – Prevents corrosion and clogging in waste heat boilers, extending equipment lifespan and improving heat recovery efficiency.。
Process Flow
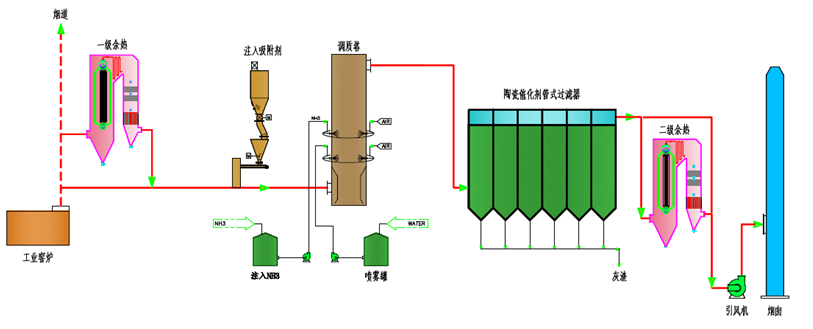
System Features
- All-in-One Purification – Simultaneous removal of NOx, SO₂, dust, and VOCs in a single reactor.
- Anti-Poisoning Ceramic Catalyst – Resists alkali metal and tar contamination, ensuring long-term stability.
- Dry Process Operation – No wastewater generation, reducing secondary pollution risks.
- Energy-Efficient Regeneration – In-situ catalyst reactivation minimizes downtime and maintenance costs.
- Adaptive to Fluctuating Conditions – Handles variable flue gas temperatures (180–400°C) without efficiency loss.